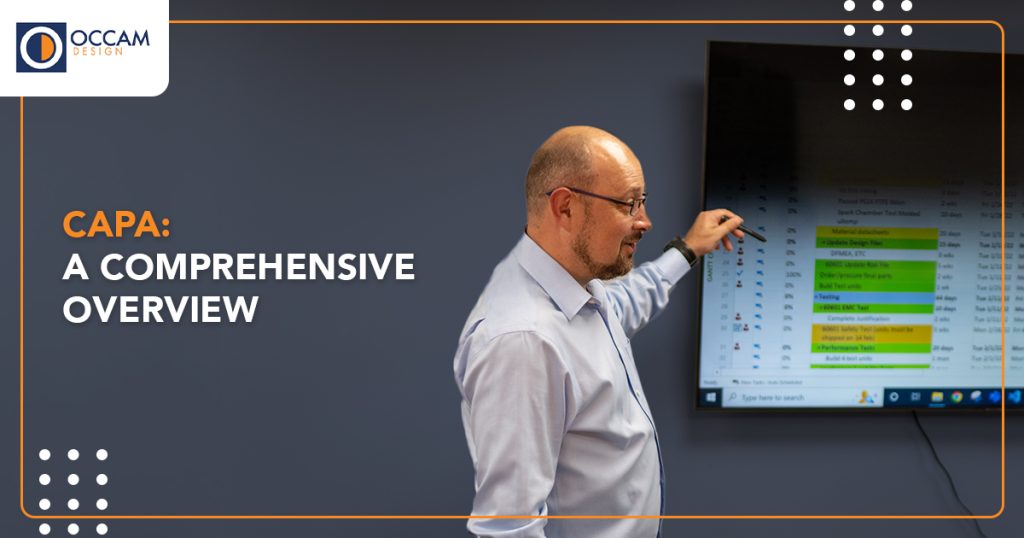
Corrective and Preventive Action (CAPA) is a fundamental component of quality management systems, particularly in the medical device industry. It involves a systematic approach to identifying, investigating, and resolving quality issues to ensure product safety and compliance with regulatory standards. CAPA processes begin with the identification of nonconformities or potential problems, followed by a thorough root cause analysis to understand the underlying issues. Corrective actions are then implemented to address and rectify existing problems, while preventive actions are designed to mitigate the risk of future occurrences. By continuously monitoring and validating these actions, companies can enhance product quality, ensure regulatory compliance, and foster a culture of continuous improvement. Effective CAPA systems not only improve customer satisfaction and trust but also lead to significant cost savings by preventing defects and reducing waste.
Understanding Capa
CAPA stands for Corrective and Preventive Actions. It is a crucial component of quality management systems (QMS) in the medical device industry. The CAPA process involves two main elements:
- Corrective Actions: Steps taken to eliminate the causes of existing nonconformities or other undesirable situations.
- Preventive Actions: Measures implemented to eliminate the causes of potential nonconformities or other undesirable situations before they occur.
Regulatory bodies such as the U.S. Food and Drug Administration (FDA) and international standards like ISO 13485 mandate the implementation of CAPA processes. These regulations ensure that medical device manufacturers systematically address quality issues and continuously improve their processes.
The Role of CAPA in Quality Management
- Identification of Issues: CAPA begins with the identification of quality issues. These can arise from various sources, including customer complaints, internal audits, production data, and regulatory inspections. Early identification is crucial for timely intervention and resolution.
- Root Cause Analysis: Once an issue is identified, a thorough investigation is conducted to determine its root cause. Tools such as Fishbone Diagrams, 5 Whys, and Failure Mode and Effects Analysis (FMEA) are commonly used to uncover the underlying reasons for the problem. Understanding the root cause is essential for implementing effective corrective and preventive
actions. - Corrective Actions: After identifying the root cause, corrective actions are implemented to address the immediate issue and prevent its recurrence. This may involve changes to processes, retraining of personnel, or modifications to the design of the medical device. The effectiveness of these actions is verified through testing and monitoring.
- Preventive Actions: In addition to addressing existing issues, CAPA also focuses on preventing potential problems. Preventive actions are proactive measures taken to identify and mitigate risks before they result in nonconformities. This proactive approach helps in maintaining consistent product quality and reliability.
- Verification and Validation: It is essential to verify and validate the effectiveness of both corrective and preventive actions. This involves monitoring the implemented actions to ensure they have resolved the issue and do not introduce new problems. Documentation of these activities is critical for regulatory compliance and continuous improvement.
Benefits of an Effective CAPA System
- Improved Product Quality: An effective CAPA system leads to higher quality medical devices by systematically addressing and preventing defects. This results in safer and more reliable products for patients and healthcare providers.
- Regulatory Compliance: Compliance with regulatory requirements is a significant benefit of a robust CAPA system. Regulatory bodies like the FDA require medical device manufacturers to have a CAPA process in place. Non-compliance can result in severe penalties, product recalls, and damage to the company’s reputation.
- Customer Satisfaction: Addressing and preventing quality issues enhances customer trust and satisfaction. When customers know that a company is committed to quality and continuous improvement, they are more likely to remain loyal and recommend the products to others.
- Cost Savings: Preventing defects and reducing waste through effective CAPA processes can lead to significant cost savings. By addressing issues early and preventing their recurrence, companies can avoid costly recalls, rework, and legal liabilities.
Challenges in Implementing CAPA
- Common Obstacles: Implementing an effective CAPA system can be challenging. Common obstacles include inadequate root cause analysis, insufficient documentation, lack of management support, and resistance to change. These challenges can hinder the effectiveness of the CAPA process and compromise product quality.
- Overcoming Challenges: To overcome these obstacles, companies should invest in training and education for their employees, establish robust documentation practices, and foster a culture of quality and continuous improvement. Management support is crucial for the successful implementation of CAPA, as it ensures the necessary resources and commitment are available.
Case Study Example
For instance, Occam Design identified a recurring issue with a specific component in one of their devices. Through a thorough root cause analysis, they discovered that the problem was due to a supplier’s inconsistent material quality. By working closely with the supplier to improve material standards and implementing additional quality checks, they were able to eliminate the issue. This not only improved the device’s performance but also strengthened Occam’s supply chain.
In conclusion, CAPA is a vital component of quality management in the medical device industry. It ensures the identification, investigation, and resolution of quality issues, as well as the prevention of potential problems. An effective CAPA system leads to improved product quality, regulatory compliance, customer satisfaction, and cost savings. Despite the challenges, companies that prioritize CAPA and foster a culture of continuous improvement can achieve significant benefits and ensure the safety and reliability of their medical devices.