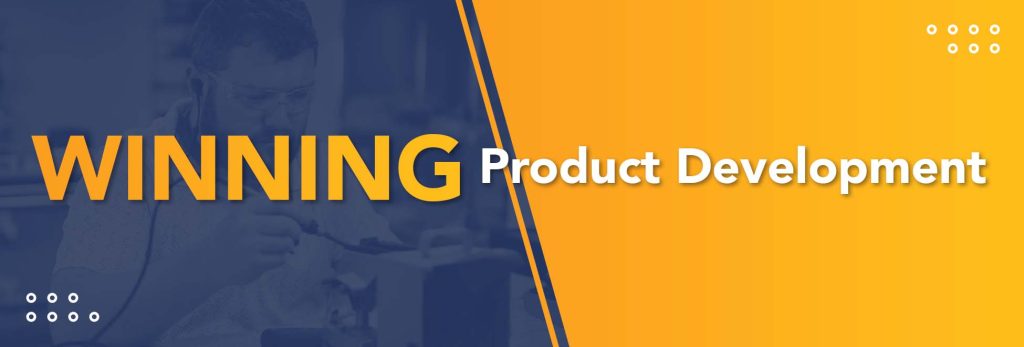
A business starts with a simple product or service idea. Maybe you came up with something while on an airplane and jotted it down on the cocktail napkin the flight attendant gave you, or perhaps you have been actively brainstorming for years to come up with something. Once you develop your idea, you need to follow a process to help you bring that product to market.

One must take the necessary steps to get their product from the infancy stages to a source of income. These processes must be followed in a logical and disciplined manner. The development phases include conceptual design, detailed design and documentation, and design verification testing pre-production and production.

Innovation is a necessary function of this process, but it will not get your product to market. Did you know that for every one hundred innovative ideas, only one is successfully brought to market? The scarcity is not in innovation but in execution. Understanding the need for innovators and executors is the difference between success and failure.
As mentioned above, successful product development requires discipline and a proven process. The ingredients for success are as follows:

This is where you define your goal in specific, quantifiable units; we will develop a product with these functions and features that will cost $X, be ready for market by Y and cost $Z to establish.

An excellent conceptual design consists of a documented, high-level, well-conceived technology plan for implementing the product that, when carefully compared against the requirements, defines the optimum approach to meeting those requirements.

The detailed design for manufacturing translates the high-level conceptual design into engineering specifications documentation and, subsequently, working units defined by the documentation. This documentation includes schematics, source code, CAD files, assembly drawings, bills of material, etc. Many inexperienced engineers consider the detailed design phase as the only step needed for product development. They tend to jump in with a “Just Do It” mentality. Their rationale, that “we don’t have the time or money for Requirements or Conceptual Design,” is flawed and has no basis in either theory or practice. There is time and place for everything. The time for detailed design is always after the requirements, and conceptual design is completed and aligned with each other.

This is the stage at which the contents of the Design History File (master book), the repository for the engineering documentation and end product of the Detailed Design stage, are used to build multiple units for comprehensive testing. These units are tested against all criteria specified in the Requirements Document to confirm that the documented design meets all its objectives.

This is where you make a small production run, give/sell to a select customer base, and the manufacturing process is validated.

This is where your hard work pays off, and you start to make money. Suppose you did all the previous steps correctly. If you skipped steps or cut corners, this is where you recognize the loss of time and money spent on development conducted without a proven process.
Leaders who wish to improve the success rate of product development are well served by ensuring they have the right combination of entrepreneurs, innovators, and product development personalities on their team. Second, they manage the inevitable tension that results when such personality types work together. When you insist that the team follows a well-defined process, this creates a more cohesive environment for all team members and creates a much better chance of success.
For a more detailed explanation of each of these steps within the process, refer to our white pages document “Keys to Successful Product Development”.
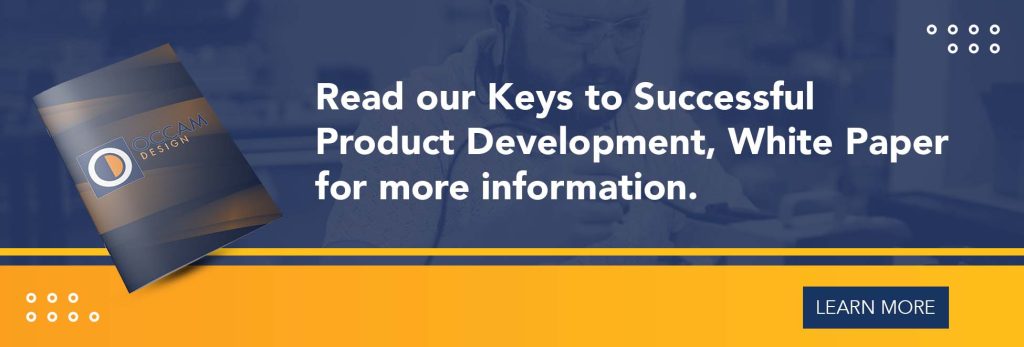